Electronics
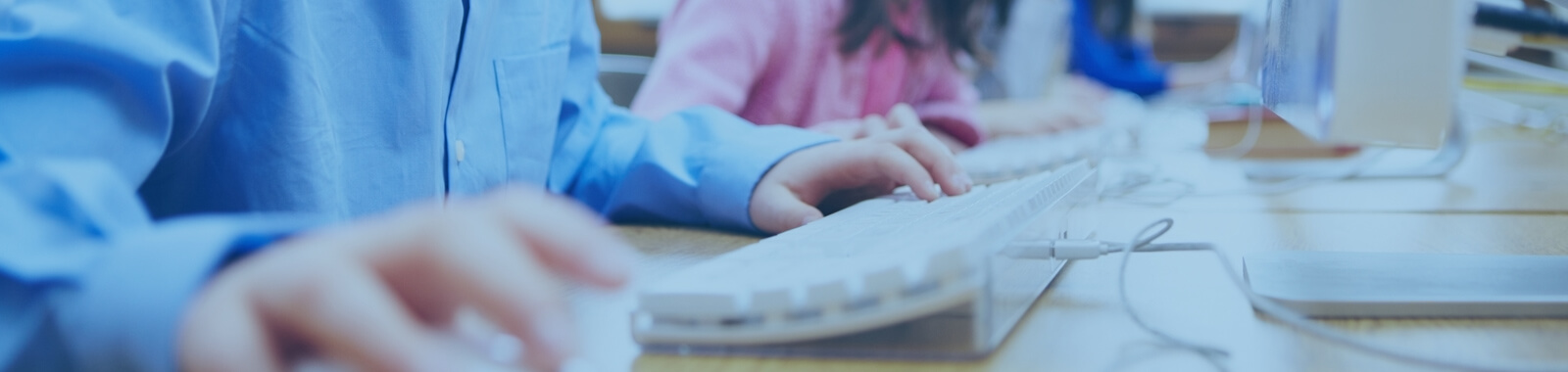
Ceramics for semiconductor manufacturing equipment
High-performance ceramics are revolutionizing semiconductor production
Fine ceramics boast outstanding heat resistance, corrosion resistance, and durability.
We at NGK group leverage these features to make a range of ceramic products for semiconductor manufacturing processes that are exposed to high-temperature corrosive gases and plasma. Our fine ceramics contain virtually no impurities which may adversely affect the semiconductors’ performance using our original hot press sintering method. The high-purity, ultra-fine crystals have outstanding dielectric strength and serve to improve semiconductor productivity. In addition to ceramic heaters and electrostatic chucks, we also manufacture chamber components made of aluminum nitride, aluminum oxide, and other materials for a range of applications.
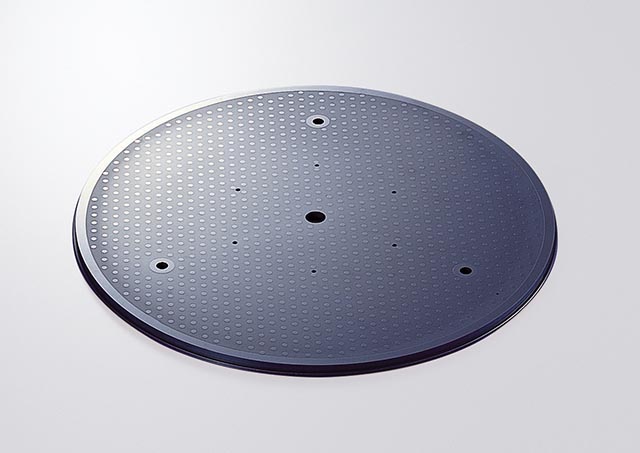
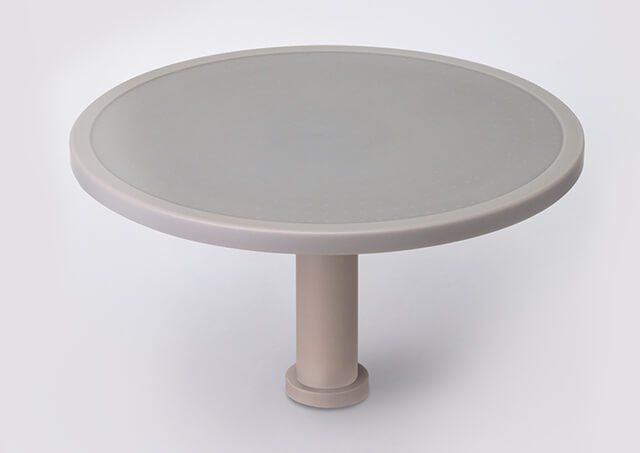
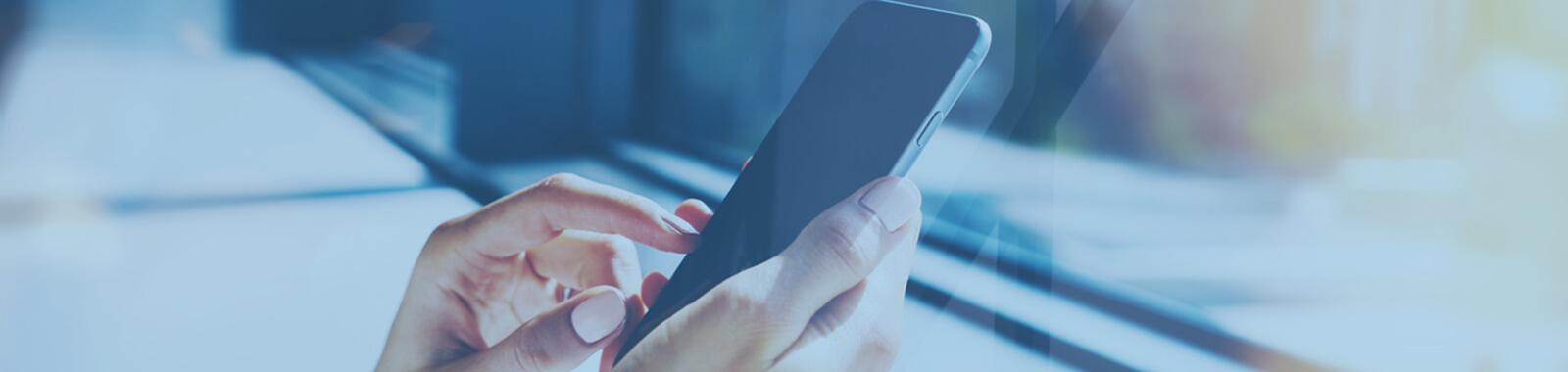
Electronic Components
Faster, smaller, more beautiful. Supporting evolution in electronics.
Today, we are witnessing the emergence of AI, the IoT and a succession of other new technologies. NGK group is supporting the evolution of electronics with advanced ceramic technologies. Our bonded wafers enable smartphones and other devices to achieve higher quality in communications and higher speeds compatible with next-generation LTE (high-speed data communications standard) and fifth-generation (5G) mobile communications systems. Developed by utilizing NGK group's proprietary ceramic technologies and featuring high heat resistance, the "EnerCera " series is an entirely new kind of battery that can be treated as an electronic component. These batteries are expected to power IoT devices, smart cards, and other next-generation devices. NGK group continues to contribute to the advancement of electronics with our innovative electronic materials and components.
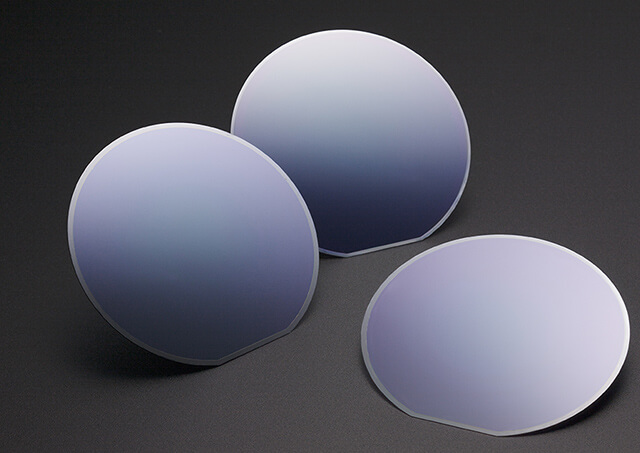
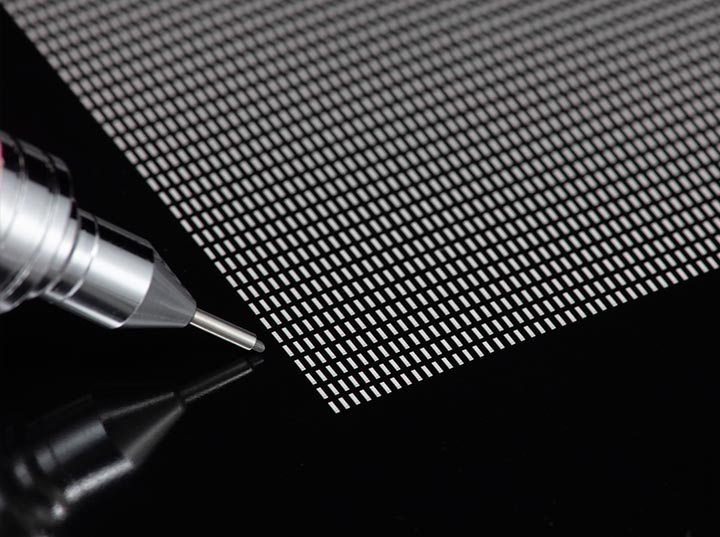
Indispensable for precise control of HDDs' magnetic heads, these ultra-compact actuators are widely used in data centers around the world as key devices in achieving both higher capacity and higher reliability of hard disk drives.
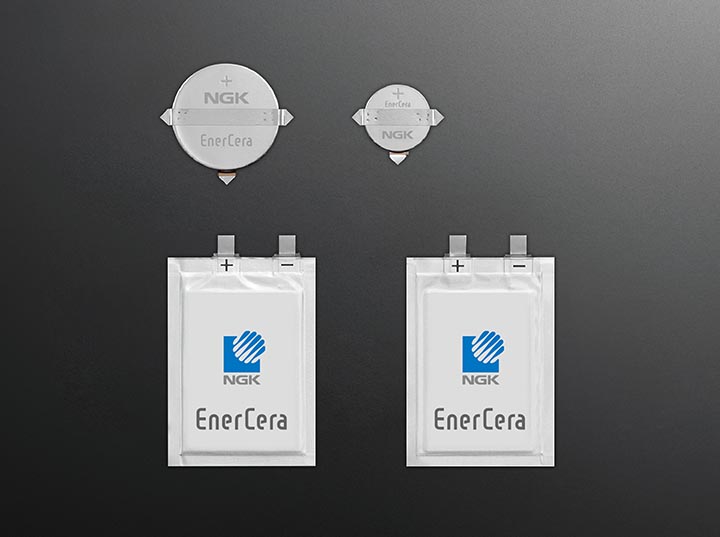
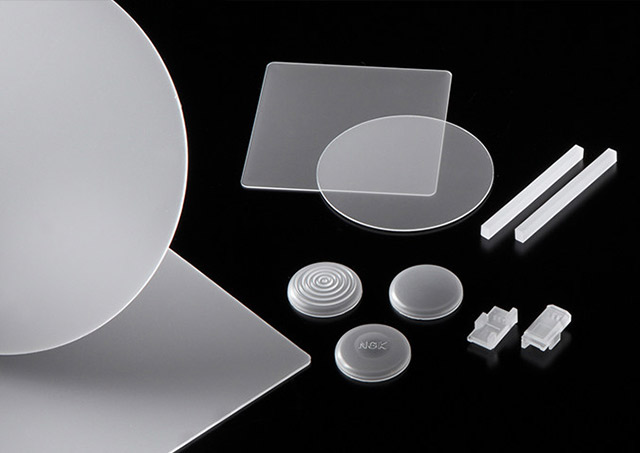
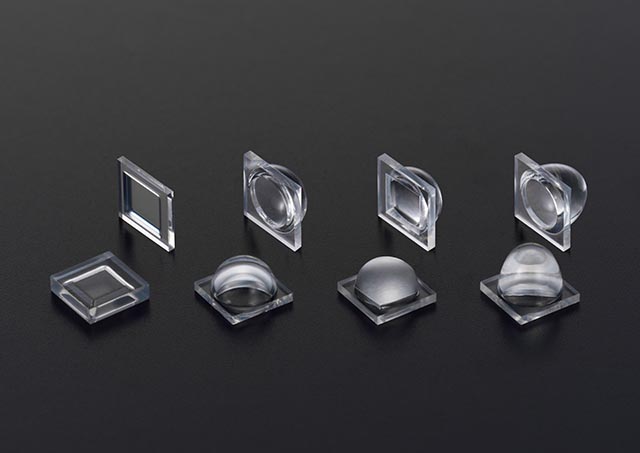
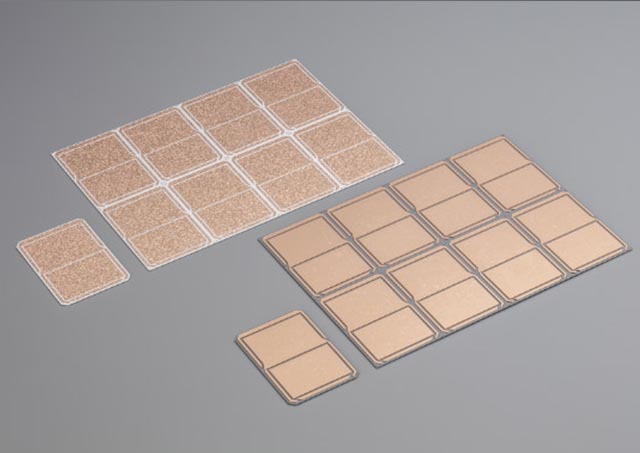
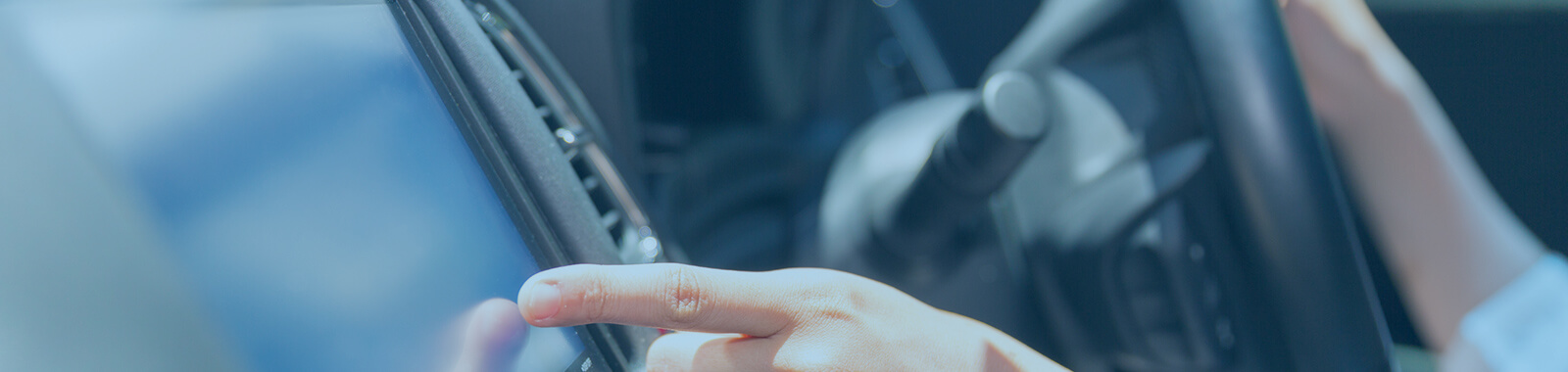
Beryllium copper
Superior strength, fatigue resistance and spring performance help make electronic devices smaller, lighter, and more reliable.
By adding a small percentage of beryllium to copper, the resulting alloy adds the strength and durability of special steel to copper’s characteristic heat and electrical conductivity. Strip and fine wires made from beryllium copper alloy are resistant to fatigue and have a long service life, making this the ideal material for reliable conductive springs and contact points in a broad range of applications, including mobile phones, household appliances, cars and industrial machinery. Here, the alloy makes a big contribution to improving reliability while reducing product size and weight. Here at NGK group, we have beryllium copper alloy production, processing and sales bases in the USA, Europe and Asia, where advanced production technologies and uncompromising quality control create products that have become sought after by the world’s industries.
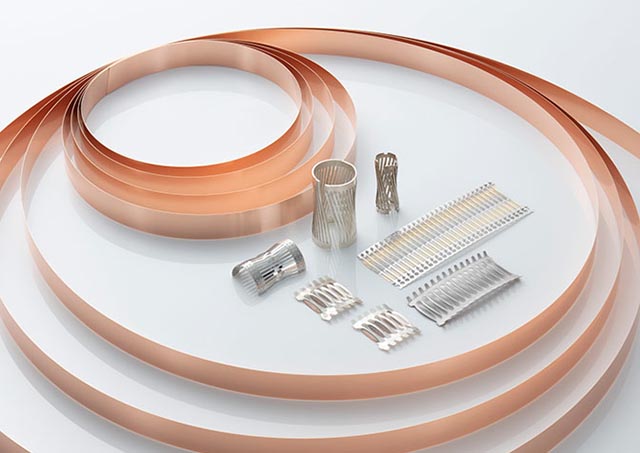
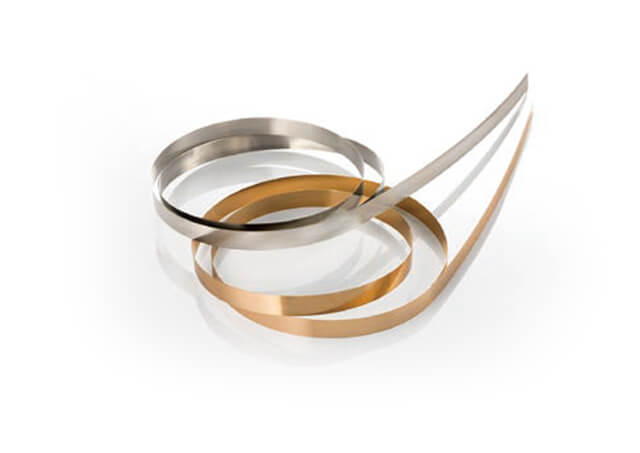